A
twin screw barrel for extruder for premixing is a machine that combines the advantages of a single screw extruder and a batch mixer. This machine is particularly suited for mixing highly viscous materials. Its design features a unique melt zone, allowing the material to be melted and then homogenized before it is injected into the die.These machines are capable of dispersive mixing and have the ability to produce high-tech precision products. The process can be controlled by several parameters, including melt temperature, vacuum level, and feed rate. Several types of twin screw barrels are available, including modular co-rotating, counter-rotating, and non-intermeshing.Twin screw machines are capable of producing a wide range of products, including plasticizers, colorants, and flavorants. They are also useful for blending, devolatilization, and polymerization.
Conical twin screw barrel for pvc pipe and pvc profile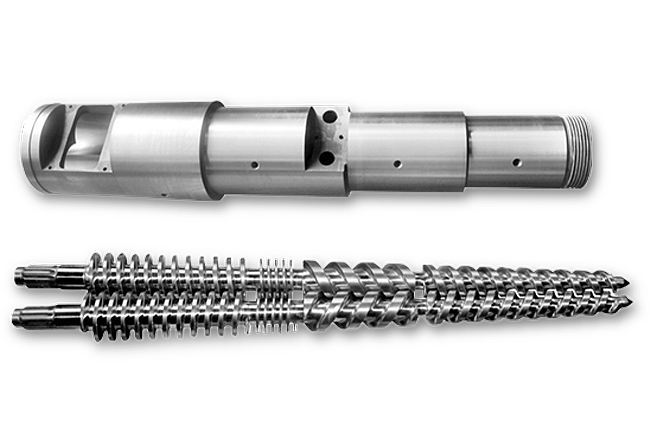
Twin screw and barrel Type: CINCINNATI, BATTENFELD, KRAUSSMAFFEI, BAUSANO, MAPLAN and AMUT model spares
There are several different techniques that are used to increase the performance of a twin screw barrel for an extruder. These techniques include adding feed streams and incorporating additional elements in the screw system.The first step is to understand the operation of a twin screw extruder. The extruder is composed of a feeding system, an extruder motor, and a pump. Materials are fed into the feeders, and the solids and liquids are pumped into the extruder. An algorithm communicates with the feeders, allowing for the control of the materials being introduced into the extruder.Twin screw extruders are classified as either co-rotating or non-intermeshing. Co-rotating screws have a more aggressive shear rate than non-intermeshing machines.Devolatilization is an essential step in the polycondensation reaction sequence. It involves the separation of volatile components from the polymer solution in the extruder.
The process is characterized by changes in the pressure and temperature in the extruder and is often used in twin screw extruders.A high-pressure polymer solution is fed into the extruder. Then the screws rotate, imparting energy to the mix. This is followed by a process known as flash devolatilization.Flash devolatilization is a vital step in the devolatilization sequence. This consists of a number of processes that remove water and volatiles from the polymer. In addition, it may be necessary for the rheology of the compound to be controlled.Twin screw barrel for reactive extruder is an important part of compounding. It is a versatile device, used for a variety of applications. The twin screw barrel can be a solid feed, liquid drain, vented or vented and side stuffing.Twin-screw extrusion was first developed more than a hundred years ago. Although it was originally intended for natural rubber/plastics applications, it is now used in numerous industries to produce highly engineered plastic products. This technology was patented by Gray M. British Patent 5056 in 1879.In addition to its applications in food, twin screw extrusion is also used for producing pharmaceutical dosage forms. Today, it is used in cutting-edge drug delivery systems. These products are made from polymer compounds that provide clarity, radiopacity, and impact resistance.The starve-feeding twin screw barrel for extruder facilitates downstream feeding. This is achieved through vents or side stuffers. It offers greater flexibility in mixing materials, and can handle several processing functions.Plastics play an important role in modern life. They are used for packaging, structural decking, car interiors, and many other applications.
In addition, they can be used to make synthetic wine corks, and in the production of fibers for carpets.Co-rotating twin screw extruders are usually found in the wood composite industry. However, they can also be found in the plastics industry, particularly in the automotive and aerospace industries.Starve-fed twin screw extruders can eliminate surging problems, and can provide more consistent feed rates. Additionally, they can provide more consistent die pressure.Twin screw extruders are widely used for manufacturing natural rubber and plastics. They are used to make everyday products, such as synthetic wine corks and space shuttle parts. Unlike other manufacturing techniques, twin screw extrusion allows for easy scale-up and continuous production.Twin screw extruders are characterized by their use of a high-speed, starve-fed design with two parallel screws rotating within a cylindrical barrel. They provide excellent mixing and forming characteristics. While they are most commonly used in the food industry, they are also used to produce structural decking and synthetic wine corks.The twin screw design consists of various screw elements including forward and reverse flights, as well as helix angles. Different screw geometries allow users to match their process to their desired application.