The biodegradable
Twin screw barrel for extruder of a main motor, a transmission box, a feeder, a screw, and a barrel. The main motor provides power energy. The gearbox distributes input shaft torque to two co-rotating output shafts. The two output shafts respectively drive the two screw rods to rotate. The feeder provides a steady flow of material to the screw. Two rotating screws drive the material forward. The material enters the tablet press from the exit of the extruder. During the conveying process, the material is sheared by the screw, exchanges heat with the barrel, and undergoes a chemical reaction. The whole process is carried out in a closed environment to reduce environmental pollution. The degradable twin-screw extruder has strong mixing ability, can realize closed continuous production, and has stable product quality. The screw has self-cleaning function, the flow path is smooth, and there is no dead angle. It does not need to clean the equipment when changing materials of different grades, and can overcome the problem of double rollers. The production of the mill has the disadvantages of high labor intensity and harsh environment.
Extruder conical twin screw barrel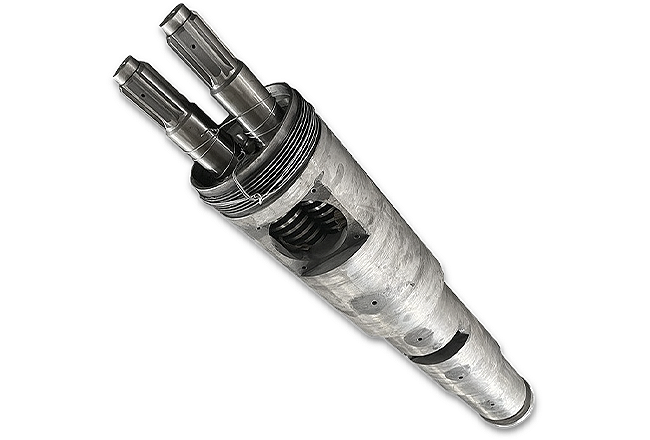
Twin screw and barrel Type: CINCINNATI, BATTENFELD, KRAUSSMAFFEI, BAUSANO, MAPLAN and AMUT model spares
The screw is the core working part of the extruder, consisting of two co-rotating screws. The screw adopts a building block structure. The two screws mesh with each other to make the flow path smooth and free of dead ends. For the mixing of thermosetting plastics, the screw is designed with four sections: sealing section, conveying section, mixing section and exhaust section. The conveying section is composed of conveying elements, which convey materials forward. For materials with low bulk density, large lead elements can be used for conveying. The length-to-diameter ratio of the screw in the mixing section is generally selected between 6 and 8. It is composed of meshing blocks, and the materials are mixed, kneaded, sheared and dispersed, and homogenized. The discharge section is composed of a conveying element and a reverse conveying element. The reverse conveying element ensures that the material is not conveyed to the end of the screw, and is extruded from the discharge port.
The screw length-to-diameter ratio is the ratio of the screw length to the screw diameter, and its value directly affects the mixing time of the material. The mixing time of thermosetting plastics needs to be appropriate. If the time is too long, the material is prone to cross-linking reaction, and if the time is short, the mixing effect will be affected. After a lot of experiments, the screw aspect ratio is generally selected between 12 and 15. The screw speed is also the main factor affecting the mixing effect. The extruder can adjust the screw speed to achieve the best effect. Generally, the screw speed is selected between 150r/min and 250r/min.