In the general screw, it is generally divided into three sections: the feeding section, the compression section, the homogenization section, and a complete set of barrels to match. First of all, we need to determine the parameters: length-diameter ratio, compression ratio, diameter, pitch, length, model brand used, number of weights, materials used and other commonly used parameters to understand. According to the difference of each model, the materials used will be different. Different materials are selected according to the materials, and their melting speed value, heat absorption performance during melting, melt viscosity, water absorption rate, thermal stability performance and other characteristics.
Single screw and barrel for injection machine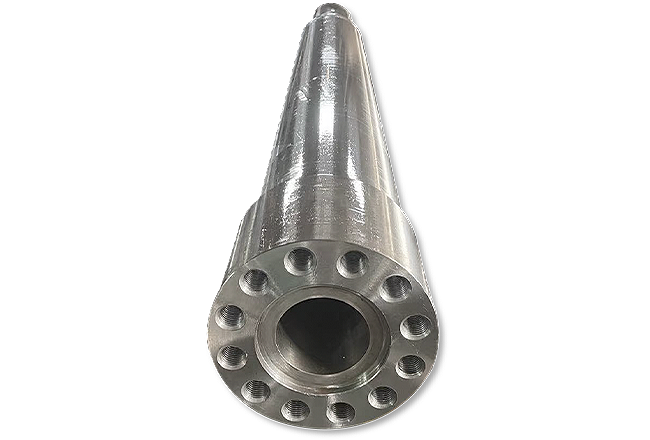
There are various differences, and the shape requirements for the plasticizing screw of the injection molding machine are very different. Even for the same plastic, due to different products, the plastics have different modifiers and fillers such as flame retardants, lubricants, glass fibers, inorganic minerals, or the requirements for color mixing and melting and homogenization are different. The shape of the granular material is different, and they all have different requirements for the screw to be selected. The screw is selected according to the model series. Since there are many types of injection molding machines, we have to choose at the beginning.
First, we must correctly judge which injection molding machine or which series the product should be produced by, such as general thermoplastic. Plastic or bakelite raw materials or PET raw materials, etc., are single-color, twin-screw, multi-color, interlayer or mixed color, etc. In addition, some products require conditions such as high stability (closed loop), high precision, ultra-high injection rate, high injection pressure or rapid production (multi-loop), and the appropriate series must also be selected to manufacture the corresponding special purpose. Diameter D, aspect ratio L/D, three lengths L1, L2, L3, screw groove depths H1 and H3 of feeding section and metering section, thread lift angle Φ (pitch S). Specifications are represented by diameter D.
Diameter grades are: 30, 45, 65, 90, 120, 150, 200, 250 and 300mm. There were changes in the design and manufacture of the rods in the earliest period, and the lengths became longer and longer according to the needs of the market and manufactured products. There are now new diameter grades with diameters 30, 45, 60, (75), 80, 90, (100), (120), (125), 150, (160), 200, 250, 300, 350, 400 and 500mm. The diameter of the forming screw produced in the industry is mostly below 300mm, while the diameter of the extruder screw used for granulation or mixing is about 150-600mm, and the largest has reached 750mm.