Bimetallic screw barrels are made of two different materials that are carefully chosen for their specific properties. The outer layer of the screw barrel is made of a high-strength alloy, such as a nickel-based alloy or a cobalt-based alloy. The inner layer, which comes into direct contact with the molten plastic, is made of a highly wear-resistant material, such as tungsten carbide.
The choice of materials for a bimetallic screw barrel is based on the specific application requirements. For example, if the plastic being processed is highly abrasive, a tungsten carbide inner layer may be chosen for its high wear resistance. If the plastic is highly corrosive, a nickel-based alloy may be chosen for its corrosion resistance.
The two materials are bonded together using a metallurgical process, such as diffusion bonding or centrifugal casting, to ensure a strong and durable bond. The bonding process allows the two materials to work together, with the outer layer providing the necessary strength and the inner layer providing the necessary wear resistance.
Overall, the materials used to make a bimetallic screw barrel are carefully selected to provide optimal performance and longevity in the specific application.
Twin extruder Bimetal screw and barrel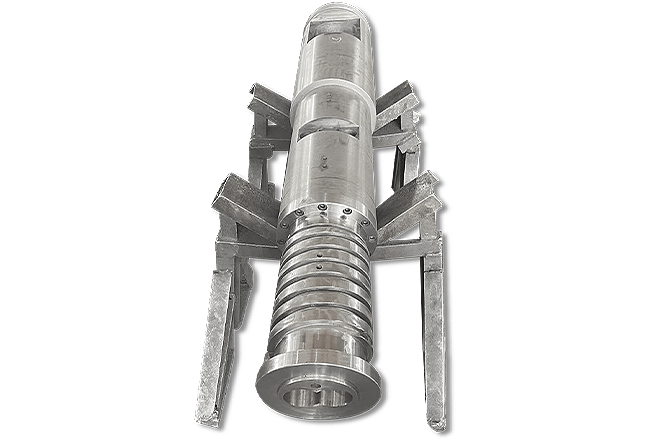
The bimetallic barrel for single screw extruder is a kind of barrel spray 2-5mm thick alloy coat on the barrel inner wall which has excellent corrosion resistance, abrasion resistance and high working temperature. And its useful service life is greatly improved contrast to common nitrided barrel. Bimetal has more obvious advantages when processing special plastics to enhance the abrasion life, such as engineering plastics, fluoride plastics, PPO etc. Our company use special alloy powders being sprayed and welded on the top of screw flights, and use different alloys and welding methods.